폐섬유에서 환금성 찾은 이동춘 리텍스 대표
봉제공장에서 배출되는 폐섬유는 골칫거리다. 작은 데다 종류까지 다양해서다. 쓰레기 취급을 받던 ‘봉제공장 폐섬유’를 자원으로 만든 이가 있다. 이동춘 리텍스 대표다. 그의 도전기다.
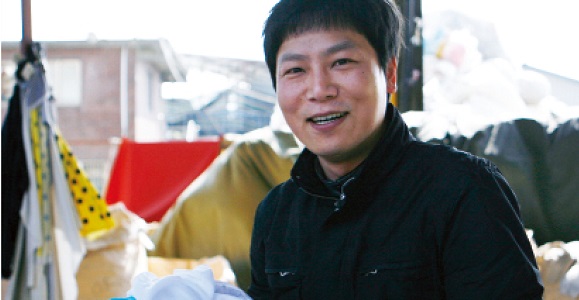
지난해 12월, 서울시청 자원순환과 간담회 자리. 부츠컷 청바지를 입은 환한 얼굴의 젊은이가 들어섰다. 이동춘(36) 리텍스 대표였다. 선한 인상이 사람들의 눈길을 사로잡았다. “봉제공장에서 섬유폐기물을 종류대로 분류만 해도 연간 300억원의 경제적 가치를 얻을 수 있습니다. 재활용률이 최대 30%까지 올라가기 때문이죠. 자원순환이라는 공익성은 물론 자연보호에도 기여할 수 있습니다. 사업제안을 검토해 주십시오.”
이동춘 대표의 발표를 들은 서울시 공무원들이 빙그레 미소를 지었다. 섬유폐기물을 줄이는 동시에 재활용률을 높일 수 있는 기회였기 때문이었다. 간담회에 참석한 서울시의 한 공무원은 “얼굴만 봐서는 패션 디자이너로 보이는데 섬유재활용 업체의 대표라니 깜짝 놀랐다”며 “자원 순환에 대한 의지가 강한 게 인상적이었다”고 말했다.
섬유재활용 업체를 운영하는 이 대표는 대기업 연구원이었다. 음식물처리 과정에서 발생하는 물질과 소재를 주로 연구했다. 그의 연구를 기반으로 개발된 김치냉장고는 공전의 히트를 쳤다. 업무는 역동적이진 않았지만 적성에 맞았다. 부족할 게 없는 생활이 3년간 이어졌다.
그런 그의 일상을 흔든 것은 뜻밖의 제안이었다. 대학시절 여행 중에 알게 된 지인이 ‘필리핀의 무인도를 인수해 관광지로 운영하는 일을 맡아 달라’고 권유한 것이다. 귀가 솔깃했다. 여행과 운동을 즐기는 삶을 꿈꾸는 그에겐 구미가 당기는 일이었기 때문이었다. 필리핀에 직접 가서 눈으로 보니 관광사업을 하기에 안성맞춤이었다. 스킨스쿠버를 운영하면 장사가 잘 될 듯 했다. 그러기 위해선 먼저 스킨스쿠버를 배워야 했다. 강사 자격증을 따기 위해 호주로 떠날 준비를 했다.
집안이 발칵 뒤집어졌다. 안정적인 직장을 나와 호주에서 아르바이트를 하면서 스킨스쿠버 자격증을 따는 게 말이 되느냐는 거였다. 그는 빙긋이 웃으며 부모를 설득했다. “1년 안에 배우고 돌아오겠다.”
호주생활은 3년 동안 이어졌다. 이유가 있었다. 생각지 못한 큰돈을 벌었기 때문이다. 영주권을 발급받은 데다 영어를 잘 했던 이 대표는 장기간 임대한 아파트의 방을 유학생에게 빌려줬다. 법을 어기지 않는 선에서 전세로 얻은 5개의 아파트도 유학생에게 임대했다. 매월 그의 손에 1000만~1500만원의 돈이 들어왔다. 이 대표는 그때 자신에게 사업수완이 뛰어나다는 사실을 깨달았다.
사업에 한창 재미를 붙이던 찰나, 집에서 호출이 왔다. 외국생활을 정리하고 들어오라는 거였다. 그의 나이 34살 때였다. 부모와의 약속을 더 이상 어길 수도 없었다. 한국으로 들어가면서 그는 중대한 결심을 했다. “한국에서 나만이 할 수 있는 사업을 해보자.”
이 대표는 그동안 관심을 갖고 있던 분야에서 사업 아이템을 찾았다. 문득 연구원 시절 접했던 음식물쓰레기가 생각났다. 재활용이나 폐기물 사업을 하면 어떨까 싶었다. 하지만 플라스틱이나 비철을 폐기하는 업체는 레드오션으로 전락한 지 오래였다. 다른 길을 찾아야 했다. 우연히 무허가로 섬유를 재활용하는 공장장을 소개받았다. 섬유쓰레기를 재활용하는 일을 하는 이였다.
음식물처리 연구하다 섬유재활용 뛰어들어
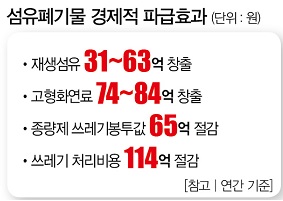
이 대표는 섬유재활용 공장을 방문하기로 했다. 의문을 풀려면 발품을 파는 수밖에 없었다. 그 공장에 들어선 순간 그는 입을 다물지 못했다. 수만t의 섬유폐기물이 거대한 산을 이루고 있었는데, 조각난 섬유가 분쇄와 침수과정을 거쳐 재활용되고 있었기 때문이다. 이 대표는 공장장에게 “왜 사업을 크게 벌이지 않느냐”고 물었다. 공장장은 고개를 절레절레 흔들며 이렇게 말했다. “공장마다 재활용을 할 수 있는 섬유가 천차만별이에요. 그래서 봉제공장에서 나오는 폐섬유는 재활용하기 어렵죠. 우리는 원단공장에서 배출되는 원단만 주로 취급합니다.”
이 대표는 속으로 쾌재를 불렀다. 그가 찾던 아이템이었기 때문이다. 봉제공장에서 나오는 폐섬유를 재활용할 수 있다면 대박을 칠 수 있다고 생각했다. 봉제공장의 폐섬유량이 원단공장보다 훨씬 많기 때문이었다.
그는 곧장 사업을 준비했다. 먼저 재활용을 위한 지침서가 필요했다. 요컨대 ‘A섬유는 B방식, 합성섬유는 C방식으로 재활용하라’는 식이었다.
이 대표의 진심을 알았는지 공장장이 함께 일하겠다며 그의 손을 잡았다. 호재였다. 이 대표는 다짐했다. “반드시 모든 섬유를 재활용하는 시대를 열겠다.”
이 대표는 2012년 리텍스를 설립했다. 경기도 남양주시에 공장도 세웠다. 그의 꿈이 시작되는 순간이었다. 리텍스는 리사이클링과 텍스타일(섬유)의 합성어다. 이 대표는 연구개발(R&D)에 착수했다. 그는 섬유에 일련번호를 매겨 종류를 나눌 생각이었다. 그럴듯한 아이디어였지만 실행에 옮기는 게 쉽지 않았다. 가지각색의 섬유를 나눠보니 종류가 수천개에 달했기 때문이다.
이 대표는 대분류-중분류-소분류로 원단을 나누기로 했다. 이를테면 이런 식이다. “천연섬유•합성섬유•원단(또는 롤) 3가지를 대분류로 삼았어요. 천연섬유에서 다시 면•울•모로 나눴죠. 면은 또다시 5가지 나눴습니다. 이런 방법으로 나눠보니 섬유를 30개로 분류할 수 있더군요. 대략적이지만 도식화를 할 수 있다는 생각이 들었죠.” 그의 생각은 맞아떨어졌다. 모든 섬유를 분류하기 어려워 ‘대•중•소 분류체계’를 만들었지만 섬유재활용의 기준으로 삼을만 했다.

폐섬유 재활용 ‘창시자’ 될까
자신감이 생긴 그는 사재를 탈탈 털어 5억원을 추가로 만들었다. 최첨단 설비를 갖추기 위해서였다. 집게차•컨베이어벨트•압축기를 구입했다. 이를 발판으로 그는 지금 꿈을 펼치고 있다. 올 1월 서울시와 ‘원단조각 쓰레기 재활용 시범사업’ 양해각서(MOU)를 체결했다. 리텍스 남양주 공장에는 하루 2만t에 이르는 서울시 폐섬유가 들어온다. 서울시도 즐거운 비명을 지르고 있다. 거의 없었던 섬유재활용률이 MOU 체결 이후 30%대로 치솟았기 때문이다. 경제적 파급효과는 월 4000만~5000만원에 달한다. 덩달아 창업 이후 6억원의 적자를 봤던 리텍스도 올 상반기 흑자전환을 기대하고 있다.
원단공장이 아닌 봉제공장에서 나오는 폐섬유를 재활용하겠다는 이 대표의 발상은 획기적이었다. ‘불가능할 것’이라는 편견을 뚫고 그는 뜻을 이뤘다. 하지만 그는 아직도 배가 고프다. 섬유재활용 과정에 또 다른 혁신을 불어넣을 연구에 몰두하고 있다. 섬유재활용에 필요한 ‘열처리 과정’을 빼버리는 게 그의 목표다. 작업시간을 단축하기 위해서다. 그의 진짜 도전은 지금부터다.
김건희 기자 kkh4792@thescoop.co.kr | @kkh4792
개의 댓글
댓글 정렬
그래도 삭제하시겠습니까?